Taxes and shipping calculated at checkout
1
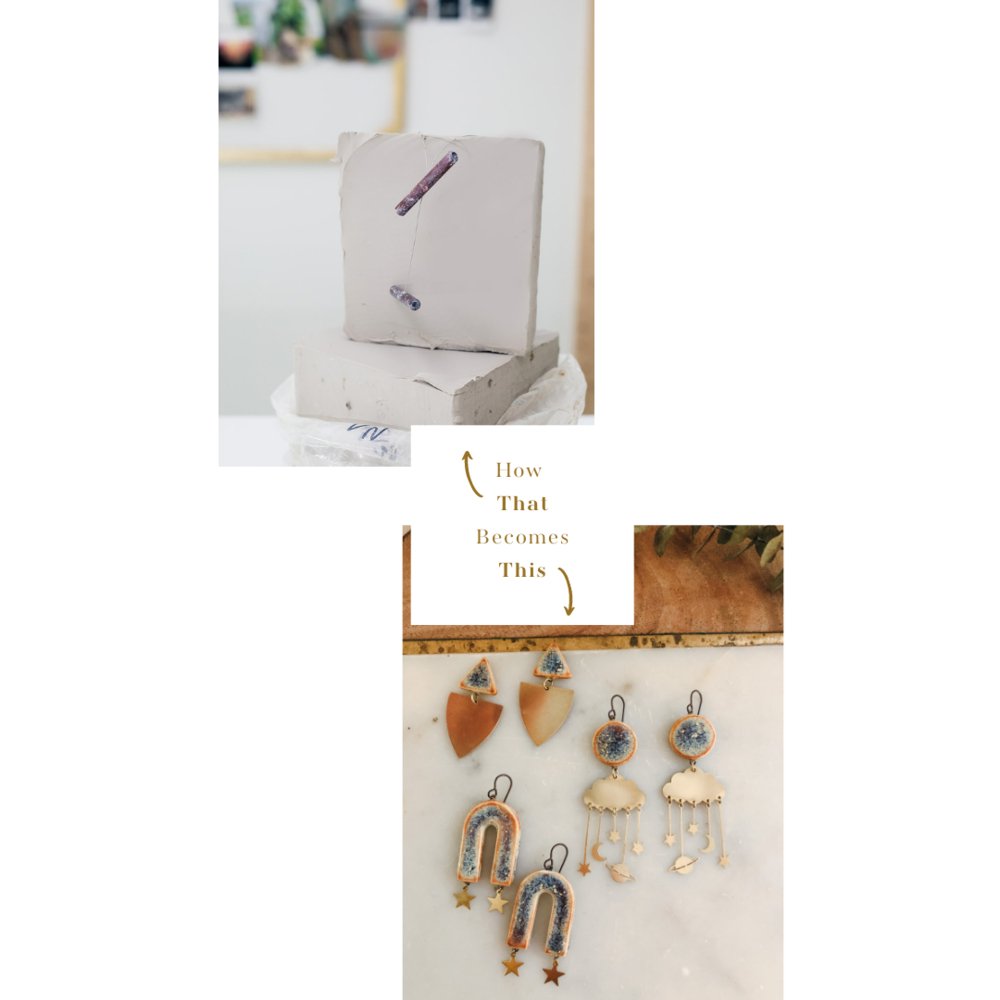
The raw clay used in the Daily Magic studio (porcelain is shown in this image) comes in 25 lb. bags. There are many transformations the clay goes through on its journey to becoming jewelry - follow along with process!
2
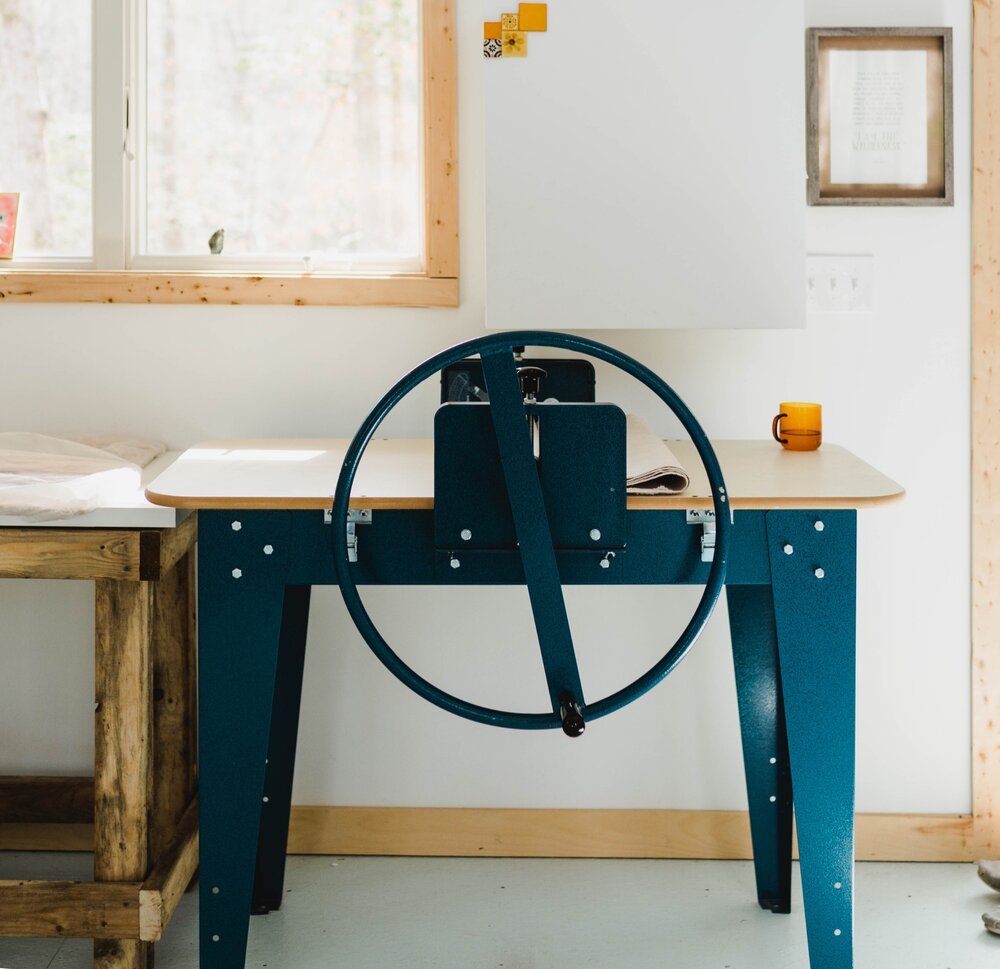
The first step in the process is rolling clay out into slabs. One of my first big investments for the studio was a slab roller.I’ve always been a hand-builder at heart and it can be very tricky to roll out uniform slabs of clay by hand. I use two types of clay in my work: ^6 porcelain and a speckled body ^6 clay (^ is...
3
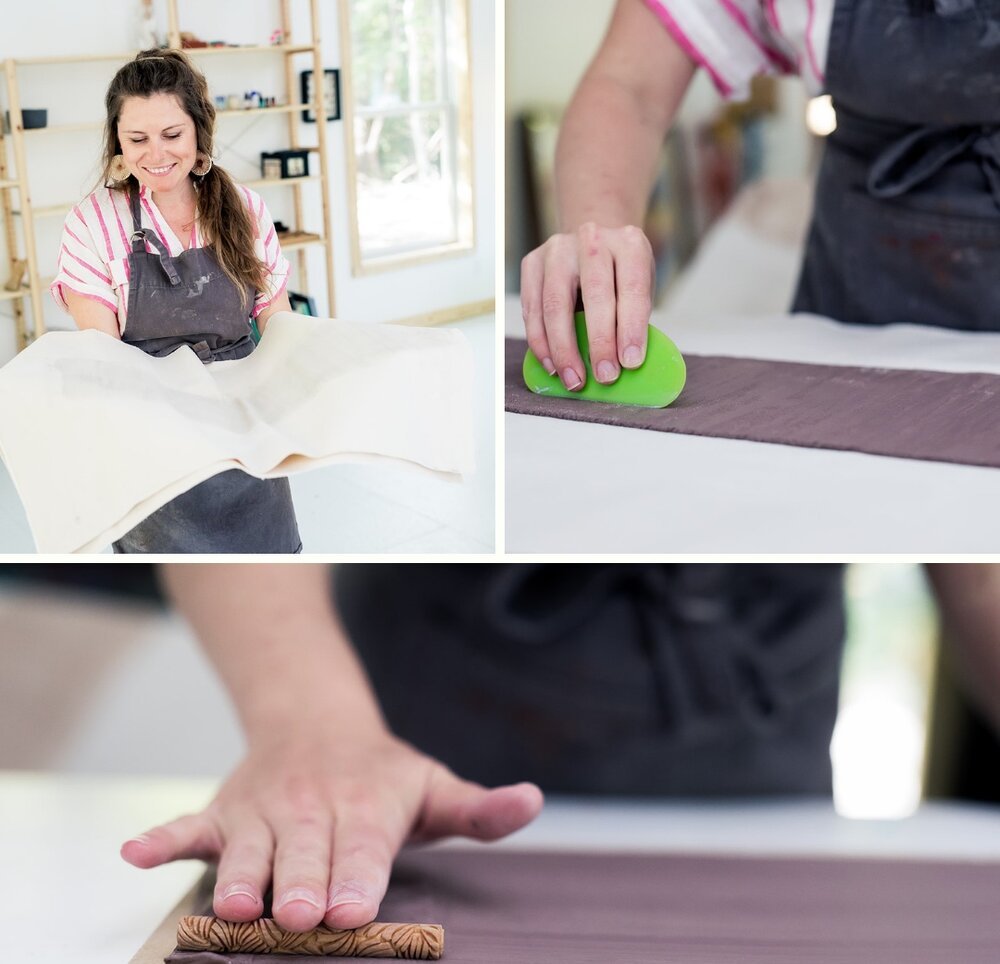
As the clay moves through the slab roller, the canvas leaves behind rough surface texture so I use a rubber rib to smooth both sides of the clay. Then I add intentional texture with a texture tool so the backside of my jewelry has interest.
4
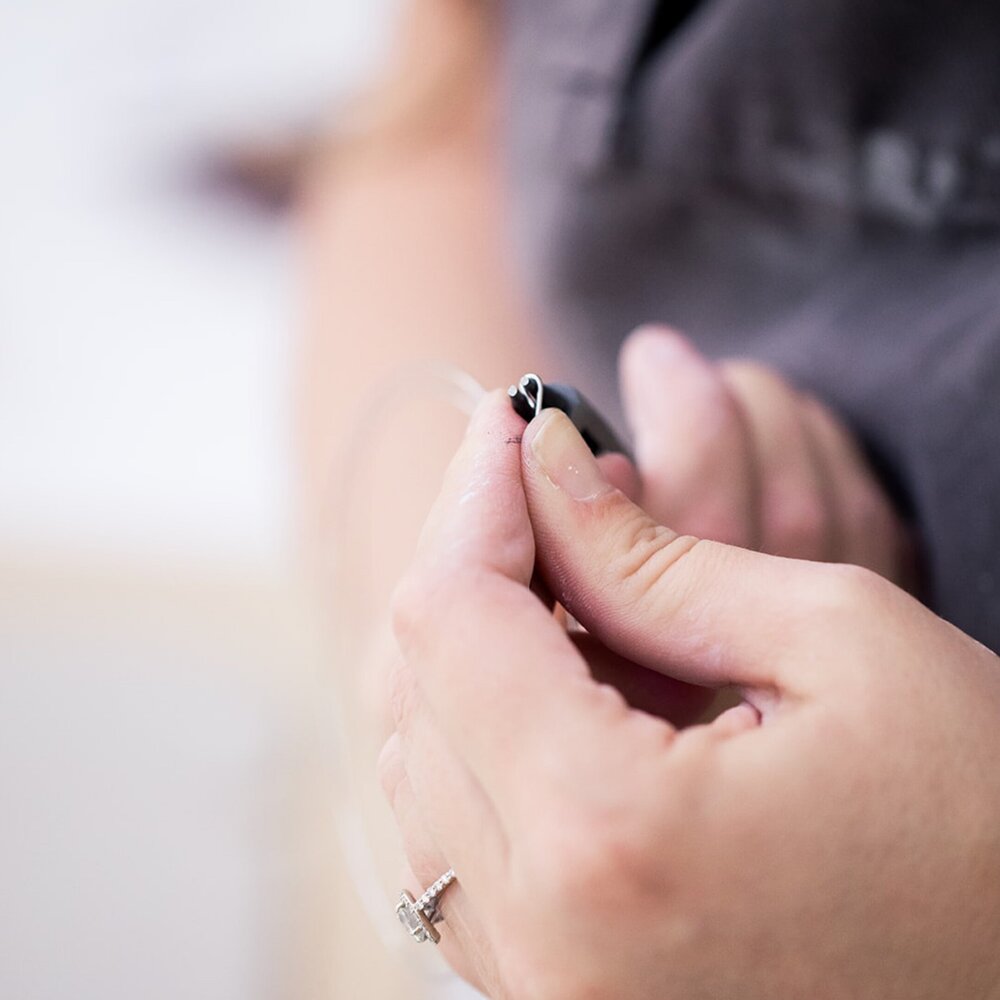
In order to attach earring hooks and charms in the later stages of the process, little wire loops need to be installed into each piece prior to drying. Each wire loop is cut and formed by hand, made from a high fire wire that can withstand the ~2,200 degrees of the kiln.
5
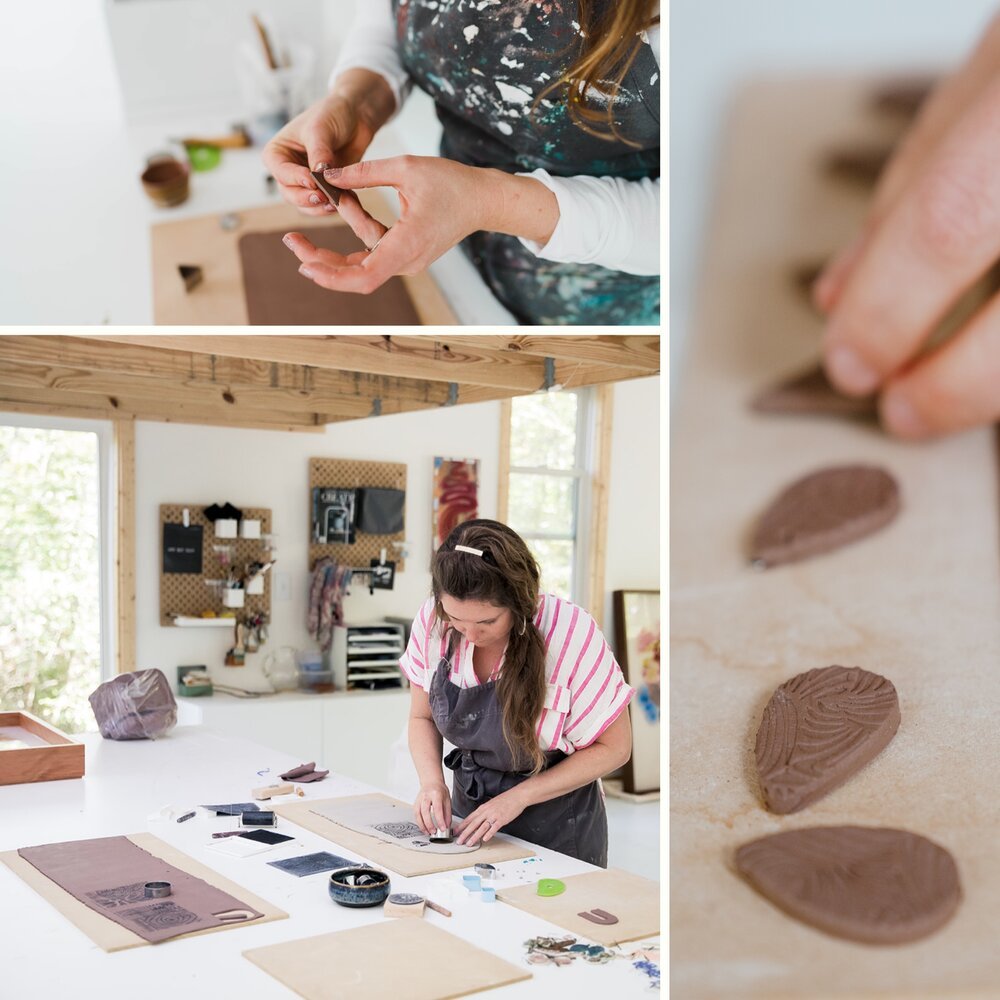
Now it is time to play! I have a whole stash of shapes, stamps and textures that I can choose from to begin transforming the clay into little pieces of art. Usually I go into this stage with a few tried-and-true designs in mind but I also leave lots of room for experimenting and trying out new combinations.
6
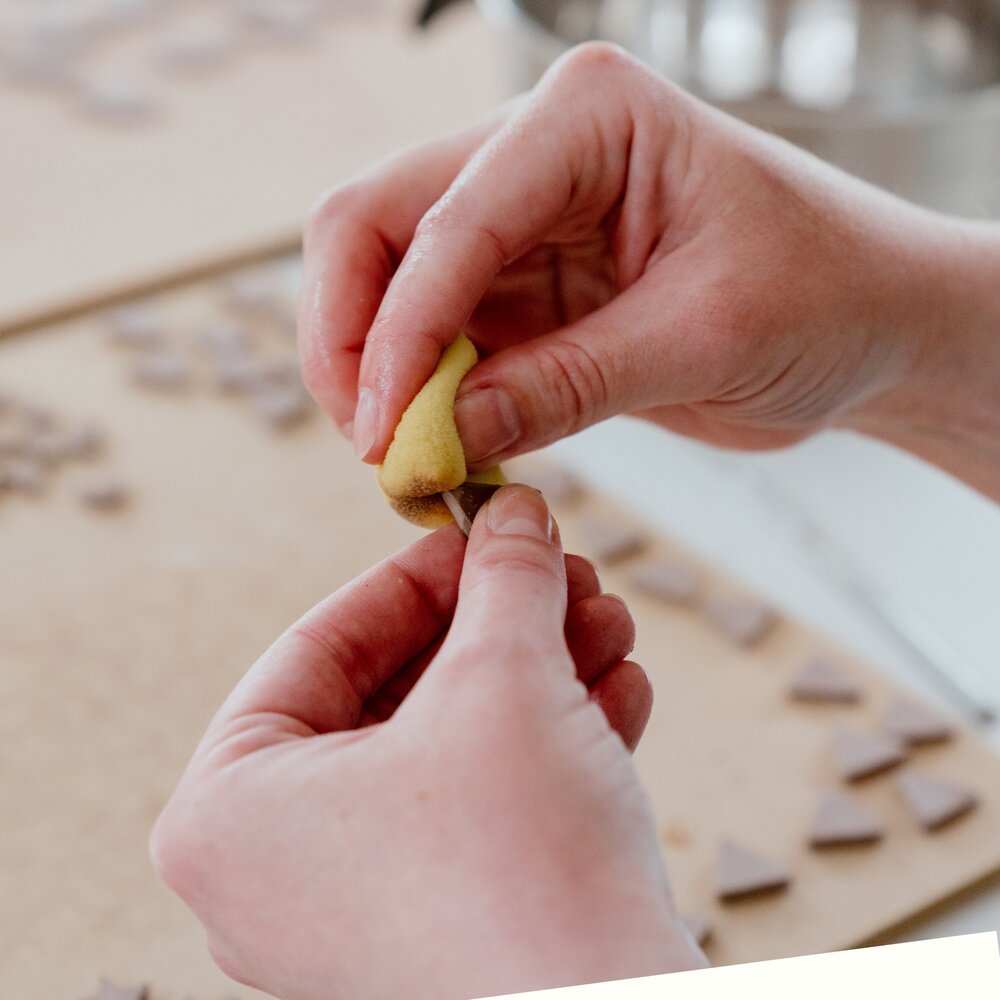
Once leather-hard (that's ceramic lingo for almost dry), every edge of every piece gets smoothed with a wet sponge. This is usually the most arduous part of the process but it’s also one of the most important, ensuring all edges are smooth and free from burrs or fractures. Once bone-dry, the pieces go through a bisque fire, which removes most of the moisture from the...
7
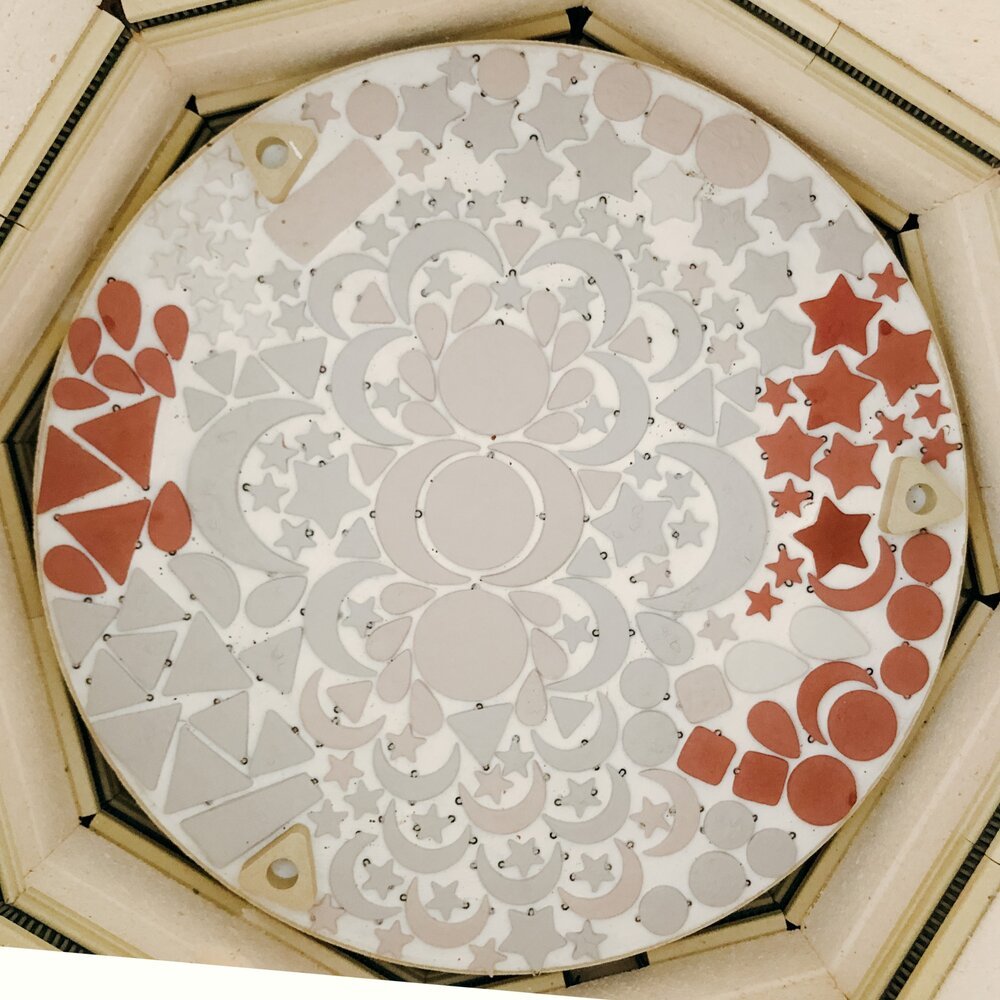
Each piece is then glazed by hand with a paint brush with at least 3 layers of glaze. Once the glaze is dry, all the pieces are mindfully arranged on kiln shelves to make use of all available space - which usually produces kiln mandalas like this one! One of my favorite parts of the entire process is creating these mandalas.
8
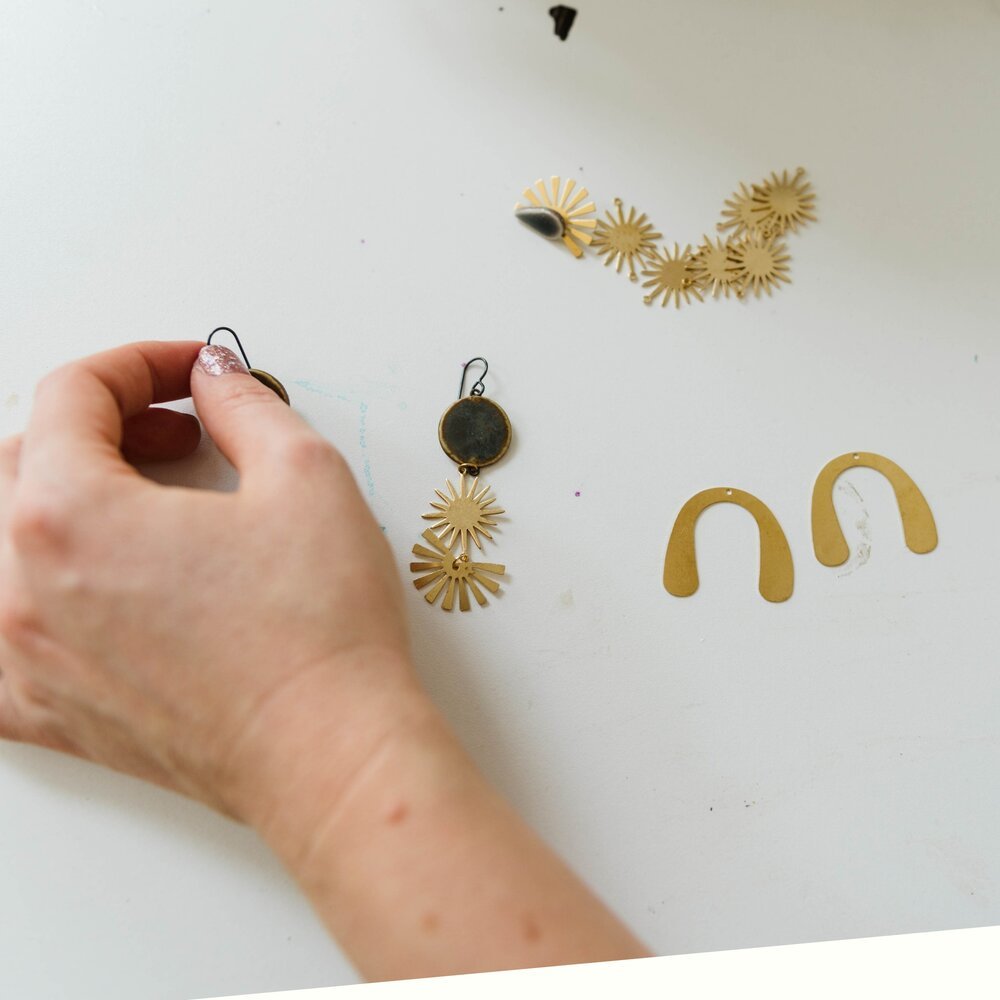
WooHoo! Now it's time for the REALLY fun part! About half of every batch of fired pieces already has an intended design but the other half is totally up for new experiments and ideas! Earring wires, studs and brass charms are all added at this final stage to create a finished set of earrings or necklace
9
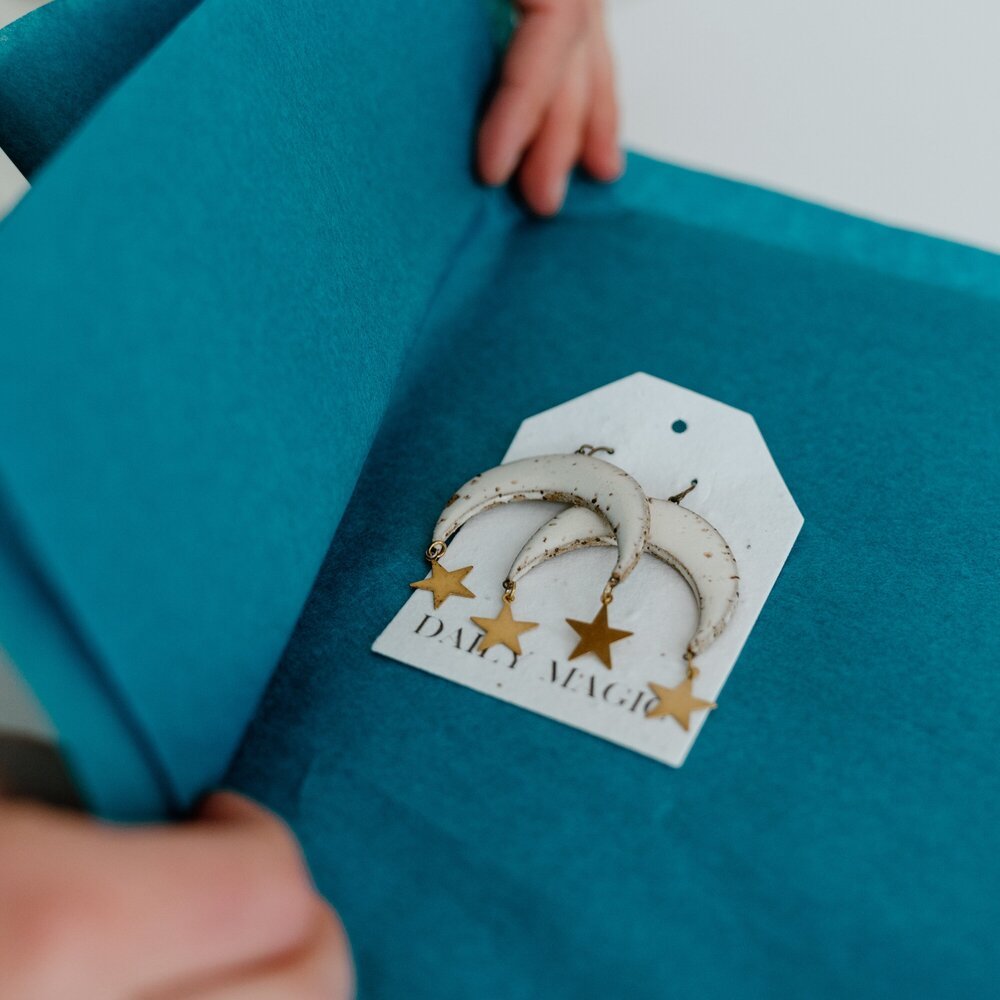
As a small business, there are a lot of hats that need to be worn. Once the creating process is complete, it's time to photograph each piece, edit the photo, and finally upload the photo to the website. When a person finds a gem they love and places an order, the item is packaged up in the Daily Magic home compostable suite (the thank you...